Maintenance management: how to share knowledge?
Mela Academy
How many times have you had to solve problems that you had already faced in the past yourself, or that your colleagues or employees had? And how much time - and money - have you lost because nobody passed on the lesson, and the knowledge remained only for those who had the direct experience in the field? Let's take a brief look at the simple, efficient ways in which we can pass on maintenance knowledge.
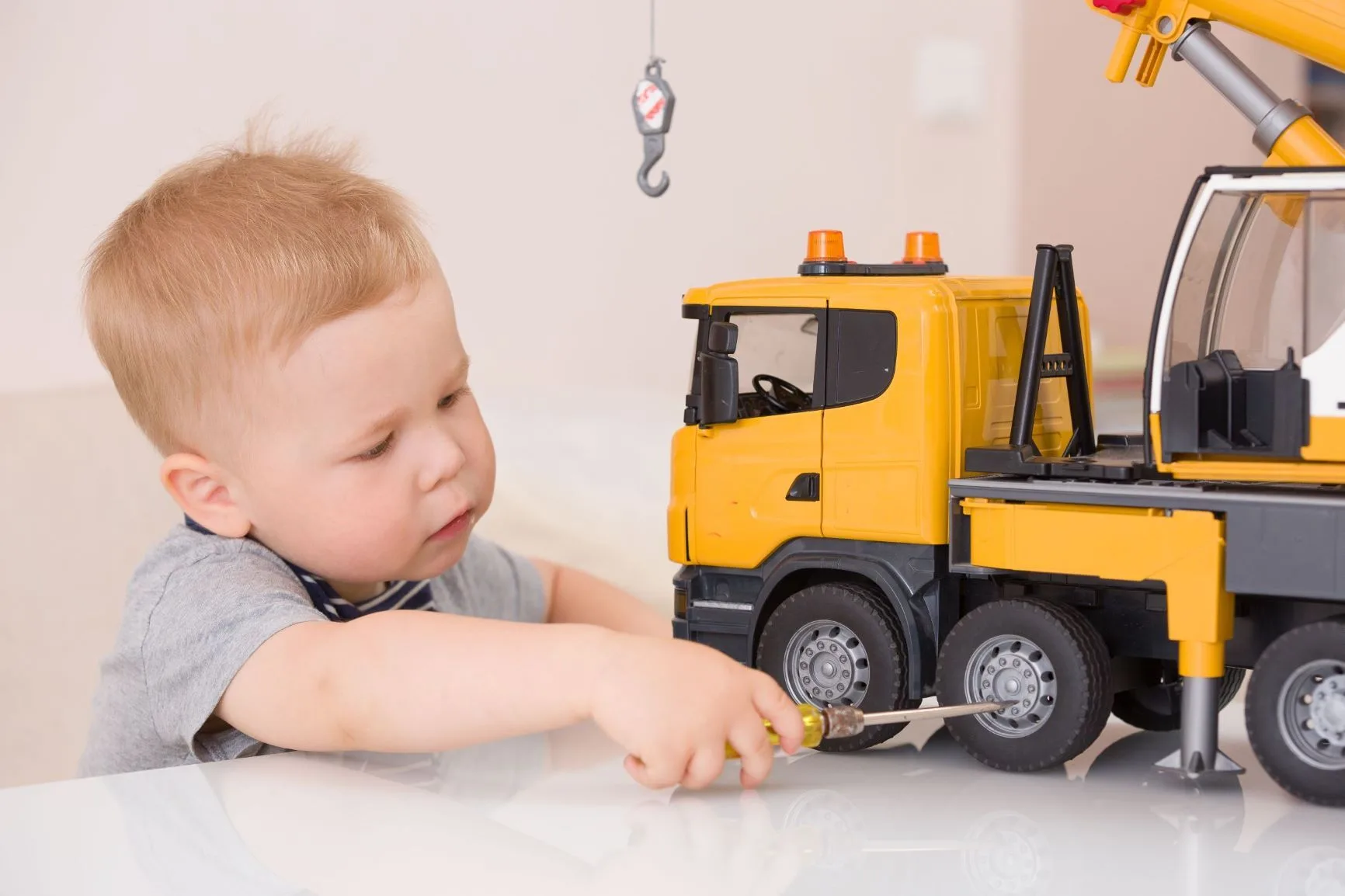
Maintenance management: how to share knowledge?
Maintenance management: how is knowledge shared?
2. How it is done today: digitalization is once again the key!
In the regions of Lombardy and Liguria, there is an expression used often in the industry: "tuca no!” This means that if something is working well, it's best to leave it alone or to think very hard before you try to fix it. This is, at first glance, a pretty simplistic rule, but in reality, it's a lot deeper than you would initially expect. Why? We are about to see the reasons.
Maintenance management: what is the impact of knowledge?
Anyone working in the field of maintenance knows how much the amount of knowledge held by people is directly proportional to the reliability of the machines. When you are setting up a maintenance squad, and formulating a process they need to follow, it will be essential to have tools to manage knowledge.
To understand this concept, you need to look at two aspects:
1. The Dunning-Kruger effect
2. The "maintenance theory"
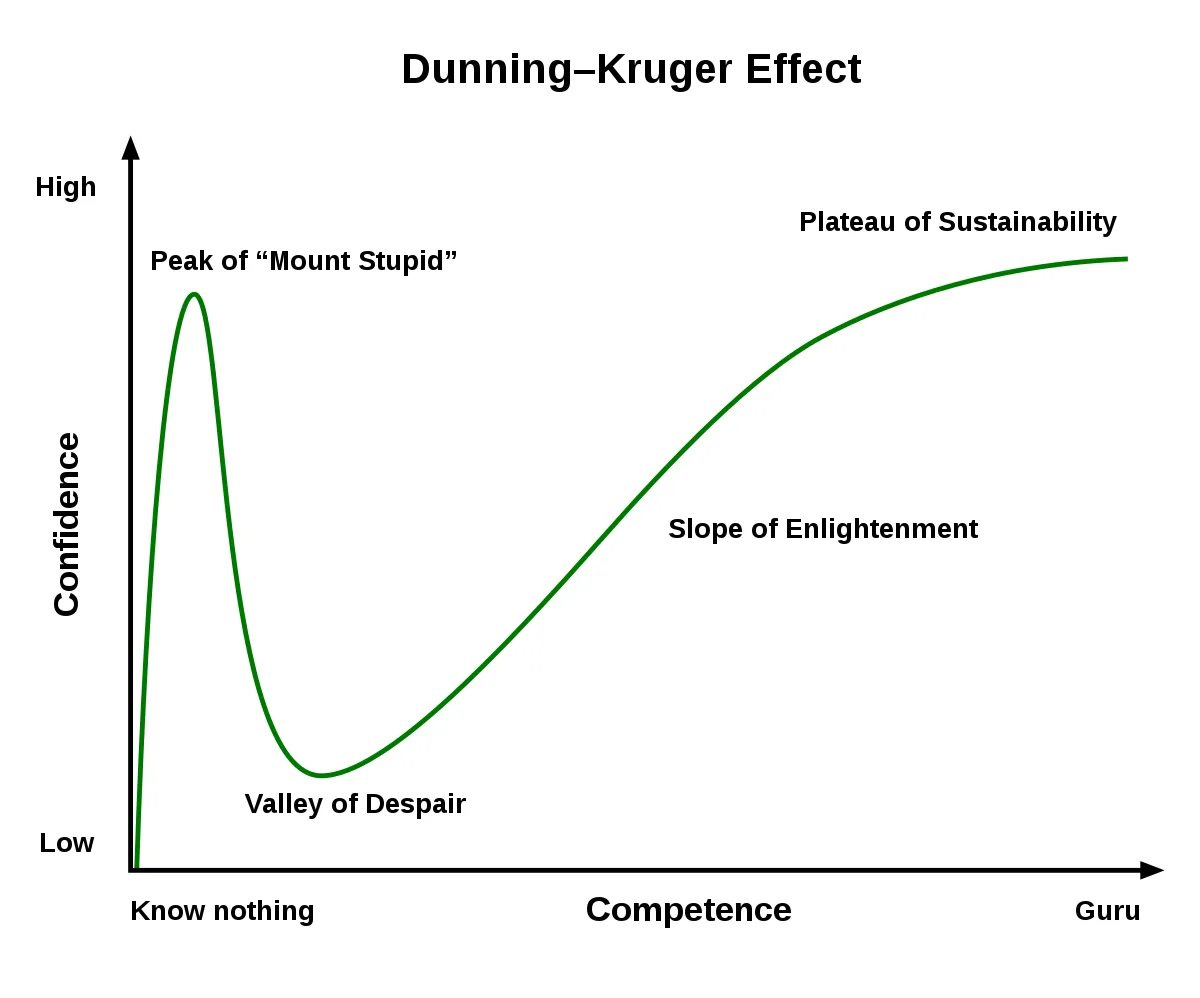
1. The Dunning-Kruger effect
The Dunning-Kruger effect is named after the two Stanford University psychologists who first described it in 1999 - the insidious cognitive distortion that causes the incompetent to remain unaware of their flaws and instead makes them consider themselves an expert.
- In this way, if you give a relatively complex task to an inexperienced maintenance technician, who means well but is clueless (and even frustrated when confronted with the complexity of this world) he will start with the best of intentions and full confidence in himself.
And the results of his work will probably be catastrophic! If the machine he was tasked with maintaining remains usable, count that as a success!
- Now, give the same task to a maintenance technician with a little bit more experience. He will start by pointing out a series of difficulties and obstacles that will keep him from completing the task. He learned his lesson when he was a newbie, but is still untrusting and fearful.
- If instead, you choose an expert maintenance technician for the same task, he will be able to explain how he would perform the task based on his experience and point out the key parts you will need to pay attention to ensure success.
2. The maintenance theory
Let's start with an existential question in the maintenance world: "why do things break?"
Let's now consider the maintenance theory using the example of a car. The answer is: things break due to 3 reasons:
- Because we use them wrongly (in the case of a car, for example, if we get involved in an accident)
- Because they degrade (wheels wear out, the oil gets burnt, friction accumulates…)
- Randomly, that is, by chance. "By chance" is only an impression. Instead, we can say that the car broke due to one of three factors.
1. Because of ageing processes that do not give any signs and cause an object to break abruptly (for example, the way semiconductors age)
2. Because of manufacturing defects, that is the imperfections or alterations that derive from an object's production.
3. Last but not least, we need to consider the possibility of human error during mounting, assembly, and installation. Human error should not be overlooked, and it is inversely proportional to the knowledge possessed by your construction and maintenance squad.
The equation is simple: the more people know, the fewer errors they make.
Experience teaches us that at least 20% of maintenance costs can be traced to errors done while mounting, assembly, and installation of machinery
If you combine both reflections, it is easy to understand why sometimes it is better to say "TUCA NO!"
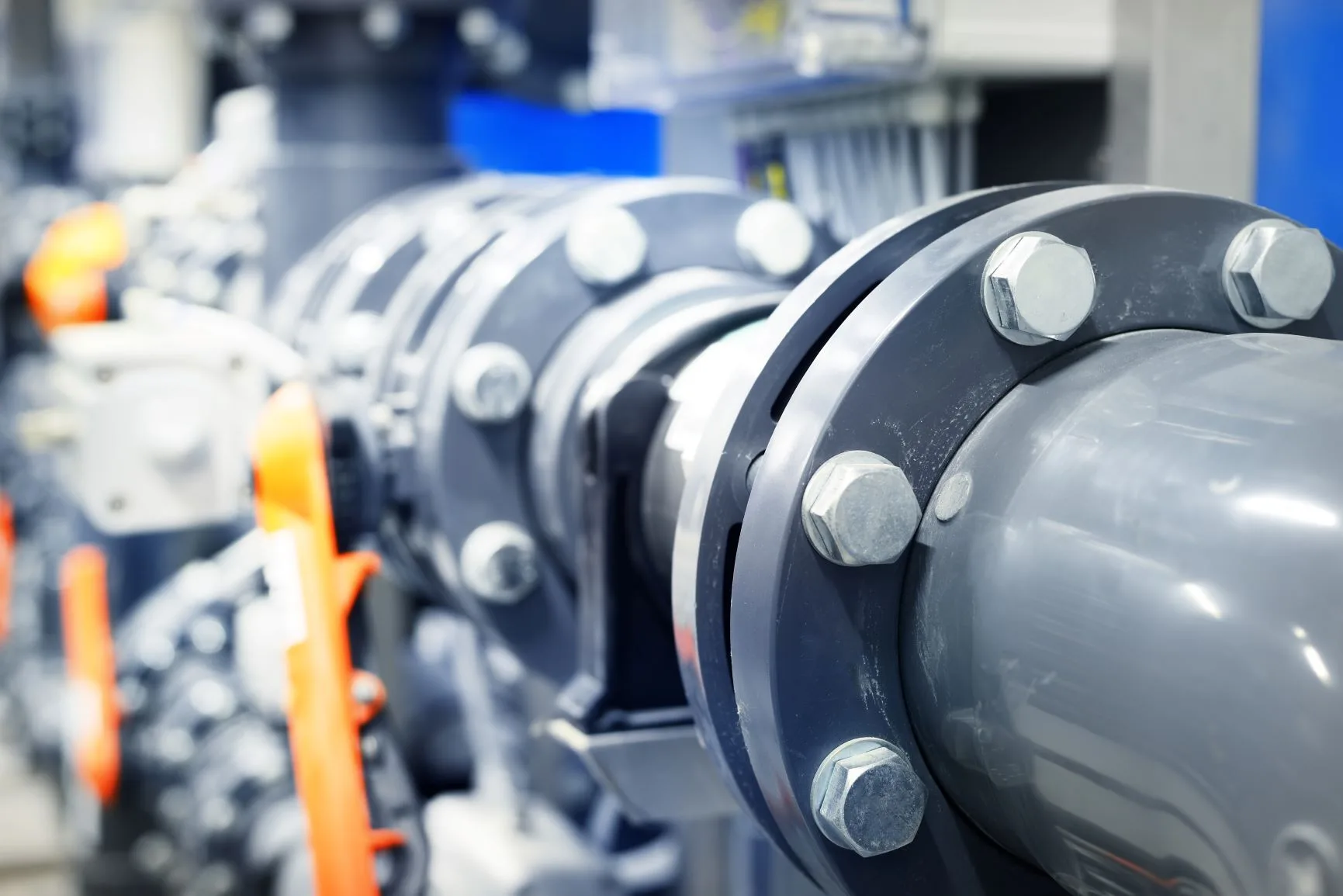
How do you share knowledge?
1. How it used to be done
A company's intellectual capital is its know-how, and such information - created, modified, shared, and used - is a valuable asset.
But how was knowledge managed and transmitted before digitalization?
To be sure, rhythms were slower, and rotation between work posts was less frenetic. It was fairly common for someone to start working at the age of 15 and to stay in the same company until it was time to retire. And in this way, they could provide their co-workers with their key contribution: their experience in the field and their problem-solving skills, because they had already seen all those problems and had solved them.
Before the digital revolution, how could you efficiently TRANSFER KNOWLEDGE?
The only way to acquire knowledge was to work in the field. It was fundamental to be present during interventions, to spot the problem to collect information and increase your experience.
To understand this, it is necessary to see what's inside the machines, to disassemble them, and to remount them step by step, to make tests and tweak the settings.
And what about passing that information, acquired slowly throughout the years, onto others? You would need to make reports and maintenance guides, which would require a significant amount of effort and would not always be successful.
Knowledge was not very formal, and instead, it was elusive and belonged to specific people. THE RISK OF LOSING IT WAS VERY HIGH!

2. How it is done today: digitalization is once again the key!
Information that cannot be found is not useful. On the other hand, digital technologies allow you to capitalize on the experiences and best practices that have already been used. This will save you money and time alike.
Thanks to Web 4.0, we have made huge strides in the field of knowledge management. Information today can be collected, saved, and made available for future activities and projects.
The cost of failing to find the information you need, alongside the time wasted trying to find them, to reconstruct it, and to repeat the work, is very high. This will leave a dent in the amount of time billed by your company
What information do you need?
- The information is collected directly in the field, while you are performing other works without the need for post-processing tasks. These can be connected directly to single machines, models, and builders.
But what instruments are good for collecting or archiving information? The answer may surprise you: to begin collecting a repository of shared knowledge, all you need is a smartphone!
1. With a smartphone, you can take pictures, make videos, and record voice notes, creating precise and error-free digital reports.
If you are going to maintain a plant, you can start by making a set of general pictures of said plant, as well as of specific components. You can also take pictures of the unmounted components, and link them to voice notes in which you narrate how you dismounted them, and which obstacles you encountered. You can also edit pictures to highlight some critical points or to draw attention to a specific component.
The people who work in the field can research and carry all this information inside their smartphones, even if they weren't present before.
In this way, we have found a way to simplify the problem of passing maintenance knowledge.
2. Use the smartphone to archive all this information in a company-owned database
You won't need to stop by the office after work to transcribe how the works were carried out, or worry about making this information thorough and understandable. The information in the smartphone can be copied automatically into the company's database.